一、引言
在工业生产中,风机和电机作为关键设备,其运行状态直接影响到生产效率和设备寿命。传统的接触式振动测量方法存在诸多局限,如安装复杂、对设备造成干扰、维护成本高等。因此,采用非接触式的激光测振传感器进行测量成为了一种理想的解决方案。本文将以实际案例为基础,详细介绍激光测振传感器在风机电机旋转振动状态非接触测量中的技术方案。
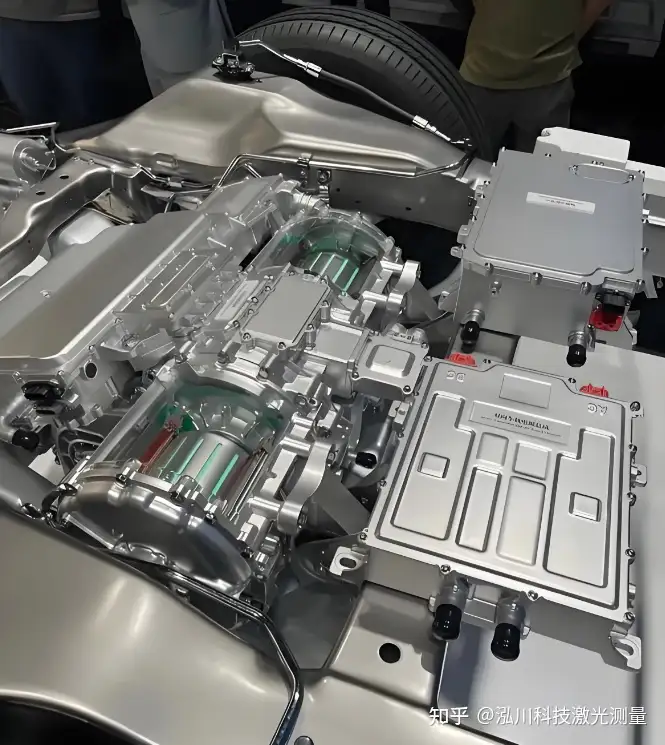
二、技术原理
激光测振传感器基于激光多普勒效应原理进行工作。当激光束照射到振动的物体表面时,反射光的频率会因物体表面的振动而发生变化。通过测量反射光与入射光之间的频率差,可以计算出物体表面的振动速度,进而分析振动状态。
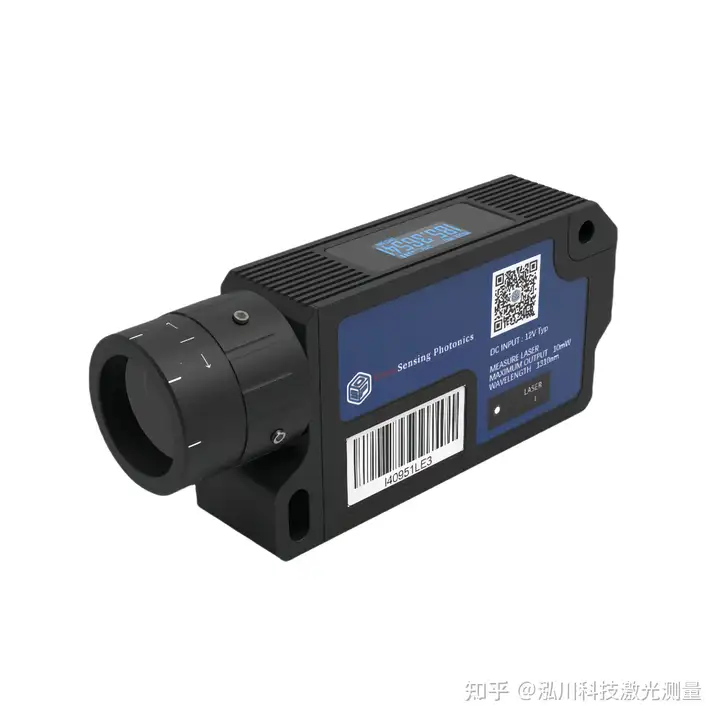
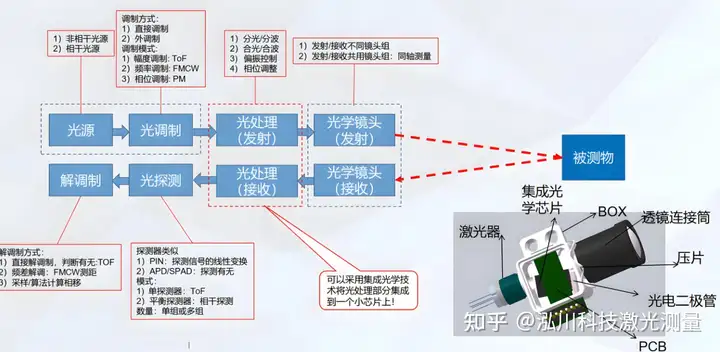
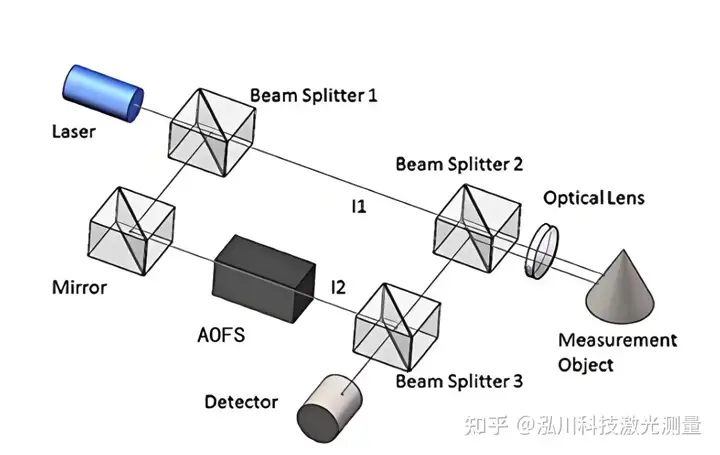
三、案例分析
1. 案例背景
某风力发电厂的风机在运行过程中出现了振动异常现象,严重影响了设备的稳定性和使用寿命。为了准确测量风机的振动状态并找出问题根源,决定采用激光测振传感器进行非接触测量。
2. 测量设备
选用MV-G100型激光测振传感器,该传感器具有外置镜头,基准距离50-2000mm,频率范围DC-1.25MHz,振动幅度分辨率<10nm,振动频率精度0.02%,最大振动量4500mm/s。

3. 测量步骤
3.1 安装与校准
将激光测振传感器固定于三脚架上,调整传感器与被测风机叶片之间的距离至合适范围(如2m)。
使用红光指引功能,确保激光束准确照射到风机叶片的预定测量点。
进行传感器校准,确保测量数据的准确性。
3.2 数据采集
启动传感器,开始实时采集风机叶片的振动数据。
设置采样频率为10kHz,以保证数据的连续性和准确性。
采集过程中,注意记录风机叶片的转速、风向等参数,以便后续分析。
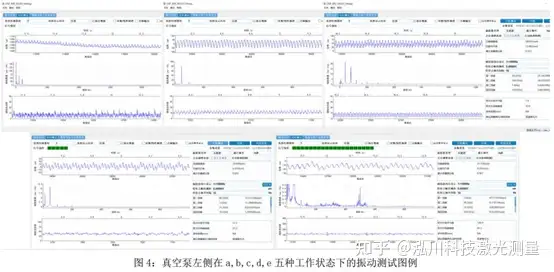
3.3 数据处理与分析
将采集到的振动数据导入专业分析软件,进行频谱分析、时域分析等处理。
通过频谱分析,可以识别出风机叶片的振动频率成分,判断是否存在异常振动。
通过时域分析,可以计算出风机叶片的振动位移、速度、加速度等参数,评估振动状态。
3.4 结果评估与优化
根据测量结果,对风机叶片的振动状态进行评估。
若发现异常振动,需进一步分析原因,如叶片不平衡、轴承损坏等。
针对问题根源,采取相应的优化措施,如调整叶片平衡、更换轴承等。
调整后再次进行测量,验证优化效果。
4. 测量结果与分析
通过激光测振传感器的测量,得到了风机叶片在不同转速下的振动数据。以下是对部分测量结果的分析:
在风机转速为15rpm时,叶片的振动频率为5Hz,振动位移为0.1mm,振动速度为0.2m/s,振动加速度为0.04g(g为重力加速度)。
在风机转速为30rpm时,叶片的振动频率为10Hz,振动位移为0.2mm,振动速度为0.4m/s,振动加速度为0.16g。
通过对比不同转速下的振动数据,发现随着转速的增加,叶片的振动频率、位移、速度和加速度均呈增加趋势。
进一步分析频谱图,发现存在频率为20Hz的异常振动成分,可能与叶片不平衡有关。
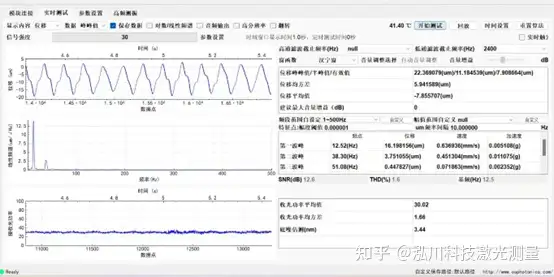
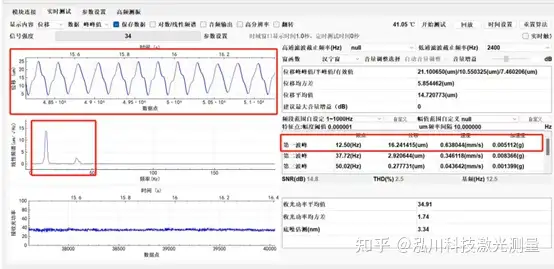
5. 优化措施与效果
针对叶片不平衡的问题,采取了调整叶片平衡的优化措施。经过调整后,再次进行测量,发现异常振动成分明显减少,振动状态得到改善。具体效果如下:
在风机转速为30rpm时,叶片的振动频率仍为10Hz,但振动位移减小至0.15mm,振动速度减小至0.3m/s,振动加速度减小至0.12g。
频谱图中异常振动成分的幅值明显降低,表明优化措施有效。
四、技术方案总结
测量设备选择:选用高精度、高稳定性的激光测振传感器,如MV-G100型。
测量步骤与方法:包括安装与校准、数据采集、数据处理与分析、结果评估与优化等步骤。
数据处理与分析:采用专业分析软件进行频谱分析、时域分析等处理,准确评估风机叶片的振动状态。
优化措施与效果验证:根据测量结果,采取针对性的优化措施,并验证优化效果。
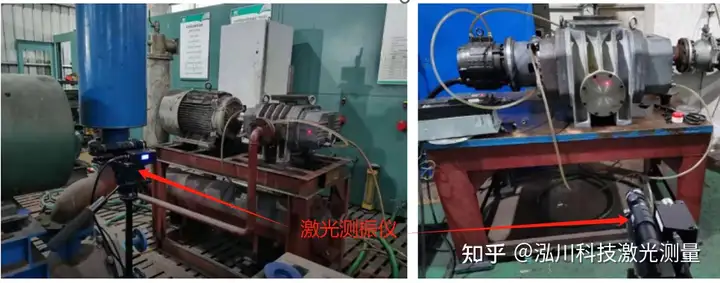
五、结论
本文详细介绍了激光测振传感器在风机电机旋转振动状态非接触测量中的技术方案。通过实际案例分析,证明了该方案的可行性和有效性。激光测振传感器具有非接触式测量、高精度、高稳定性等优点,在工业生产中具有广泛的应用前景。随着技术的不断发展,激光测振传感器将在更多领域发挥重要作用。