四、测量精度影响因素及优化策略
4.1 影响测量精度的因素分析
在光谱共焦传感器测量晶圆厚度的过程中,测量精度受到多种因素的交织影响,这些因素犹如精密仪器中的细微瑕疵,虽小却足以对测量结果产生显著的偏差。
光源稳定性是影响测量精度的关键因素之一。光源作为整个测量系统的能量源头,其输出光的强度和波长稳定性直接关系到测量的准确性。若光源输出光强度出现波动,就如同水流的忽大忽小,会导致反射光信号的不稳定,进而影响探测器对反射光波长的准确测量。在实际应用中,由于光源的老化、电源的不稳定等原因,都可能导致光源输出光强度的波动。而光源波长的漂移则会使测量系统对距离的计算产生偏差,就像尺子的刻度发生了变化,从而影响测量精度。温度变化、光学元件的热膨胀等因素都可能引发光源波长的漂移。
光学系统像差也是不可忽视的影响因素。光学系统中的物镜、透镜等元件在制造和装配过程中,不可避免地会存在一定的像差,如球差、色差、像散等。这些像差会使光线的传播路径发生偏离,导致聚焦不准确,从而影响测量精度。球差会使光线在焦点处形成一个弥散斑,而不是一个理想的点,这会降低测量的分辨率;色差则会使不同波长的光聚焦在不同的位置,导致测量系统对波长的判断出现误差。此外,光学元件的表面质量和清洁度也会对测量精度产生影响。表面的划痕、灰尘等会散射光线,降低光信号的强度和质量,进而影响测量结果。
探测器噪声同样会对测量精度造成干扰。探测器在将光信号转换为电信号的过程中,会引入各种噪声,如热噪声、散粒噪声、读出噪声等。这些噪声会使探测器输出的电信号出现波动,就像平静的湖面泛起涟漪,导致测量结果的不确定性增加。在测量微弱的反射光信号时,探测器噪声的影响尤为明显。热噪声是由于探测器内部的电子热运动产生的,散粒噪声则是由于光信号的量子特性引起的,读出噪声则与探测器的读出电路有关。
环境温度和振动也会对测量精度产生不容忽视的影响。温度的变化会导致光学元件的热膨胀和收缩,从而改变光学系统的焦距和光路长度,进而影响测量精度。在高温环境下,光学元件的热膨胀可能会导致物镜的焦距发生变化,使聚焦不准确。此外,温度变化还会影响光源的输出特性和探测器的性能。振动则会使光学系统中的元件发生位移和晃动,导致光信号的不稳定和测量误差的增加。在实际的半导体制造车间中,机械设备的运转、人员的走动等都可能产生振动,这些振动会通过工作台传递到测量系统中,影响测量精度。
4.2 误差补偿与精度提升方法
为有效克服上述影响测量精度的因素,一系列误差补偿与精度提升方法应运而生,这些方法犹如精密仪器的 “调试工具”,能够显著提高光谱共焦传感器测量晶圆厚度的准确性和可靠性。
针对光源稳定性问题,采用先进的温度补偿算法。温度的变化会对光源的输出特性产生显著影响,导致光强度和波长的波动。通过在光源内部集成高精度的温度传感器,实时监测光源的温度变化。当温度发生改变时,传感器将温度信息反馈给控制系统,控制系统根据预先建立的温度与光强度、波长的关系模型,自动调整光源的驱动电流或其他相关参数,以补偿温度变化对光源输出的影响。若温度升高导致光源波长发生漂移,控制系统可以通过调整驱动电流,使光源的波长恢复到正常范围,从而确保光源输出的稳定性。
为减少环境振动对测量精度的干扰,在测量系统中安装高精度的振动隔离装置。这种装置通常采用空气弹簧、橡胶垫等材料,能够有效地吸收和隔离外界的振动。空气弹簧具有良好的弹性和阻尼特性,可以在一定程度上缓冲振动的传递;橡胶垫则能够进一步减小振动的幅度。在实际应用中,将测量系统放置在振动隔离平台上,平台通过空气弹簧与地面隔离,橡胶垫则用于增加平台与测量系统之间的阻尼。这样,即使在振动较为剧烈的环境中,测量系统也能保持相对稳定,减少因振动引起的测量误差。
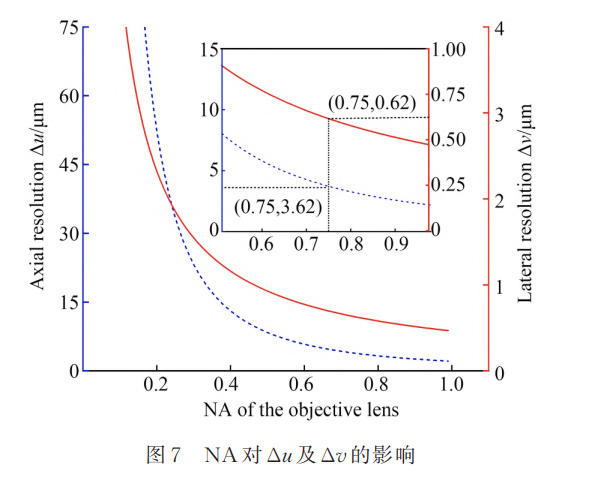
对光学系统进行优化设计,也是提升测量精度的重要举措。在设计过程中,采用先进的光学仿真软件,对光学系统的像差进行精确分析和校正。通过调整物镜的曲率半径、折射率分布等参数,优化光学系统的结构,以减小像差的影响。还可以采用消色差透镜、非球面透镜等特殊光学元件,进一步提高光学系统的成像质量。消色差透镜能够有效消除色差,使不同波长的光聚焦在同一位置;非球面透镜则可以减小球差和像散,提高光学系统的分辨率和聚焦精度。
在数据处理阶段,采用先进的算法对测量数据进行滤波和修正。常见的滤波算法有卡尔曼滤波、中值滤波等。卡尔曼滤波算法能够根据测量数据和系统的状态模型,对测量结果进行最优估计,有效地去除噪声干扰;中值滤波算法则通过对测量数据进行排序,取中间值作为滤波后的结果,能够去除数据中的异常值。通过建立测量误差模型,对测量数据进行修正,进一步提高测量精度。在建立误差模型时,充分考虑光源稳定性、光学系统像差、探测器噪声等因素对测量结果的影响,通过实验数据和理论分析,确定误差模型的参数,从而实现对测量数据的准确修正。
4.3 实验验证与结果分析
为了全面验证优化策略的有效性,精心设计并实施了一系列严谨的实验。在实验中,选取了具有代表性的不同材质和厚度的晶圆作为测试样本,这些晶圆涵盖了常见的半导体材料,如硅、砷化镓、氮化镓等,其厚度范围也覆盖了半导体制造中常见的尺寸。
在实验过程中,分别使用优化前和优化后的光谱共焦传感器测量系统对晶圆厚度进行测量。对于每一种晶圆样本,都进行了多次重复测量,以确保测量结果的可靠性和准确性。在优化前的测量中,由于受到多种因素的影响,测量结果存在一定的波动和误差。例如,在测量硅晶圆时,测量精度约为 ±0.5μm,且不同测量点之间的重复性较差,标准差达到了 0.1μm 左右。这主要是由于光源稳定性不足,导致反射光信号波动较大,以及光学系统的像差使得聚焦不够准确,从而影响了测量精度。
在采用了上述优化策略后,再次对相同的晶圆样本进行测量。结果显示,测量精度得到了显著提升。在测量硅晶圆时,测量精度提高到了 ±0.1μm 以内,重复性也得到了极大改善,标准差降低至 0.02μm 左右。这一结果表明,优化后的测量系统能够更准确地测量晶圆厚度,并且在不同测量点之间的一致性更好。
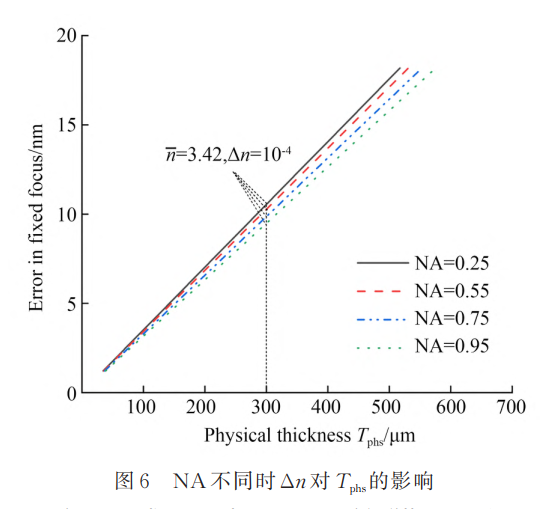
通过对实验数据的详细分析,可以清晰地看到优化策略的显著效果。在光源稳定性方面,采用温度补偿算法后,光源输出光强度的波动明显减小,波长漂移也得到了有效控制。这使得反射光信号更加稳定,探测器能够更准确地测量反射光的波长,从而提高了测量精度。在光学系统优化方面,通过调整物镜的参数和采用特殊光学元件,像差得到了有效校正,光线的聚焦更加准确,进一步提高了测量精度。在数据处理方面,采用先进的滤波和修正算法,有效地去除了噪声干扰,减小了测量误差,使测量结果更加准确可靠。
为了更直观地展示优化前后测量精度的变化,绘制了测量精度对比图。从图中可以明显看出,优化后的测量精度曲线更加集中,波动更小,表明测量结果更加稳定和准确。在测量不同材质的晶圆时,优化后的测量系统都能够显著提高测量精度,满足半导体制造对高精度测量的严格要求。
通过本次实验验证,充分证明了所提出的优化策略能够有效地提高光谱共焦传感器测量晶圆厚度的精度和可靠性。这些优化策略不仅在理论上具有重要意义,而且在实际应用中也具有很高的实用价值,为半导体制造过程中的晶圆厚度测量提供了更可靠的技术支持。
五、实际应用案例深入解析
5.1 案例一:某半导体企业晶圆生产
某半导体企业在其晶圆生产过程中,引入了光谱共焦传感器来测量晶圆厚度,这一举措为企业的生产带来了显著的变革。该企业主要生产用于高端电子产品的集成电路晶圆,随着市场对产品性能和质量要求的不断提高,对晶圆厚度的精确控制成为了生产过程中的关键环节。
在引入光谱共焦传感器之前,该企业采用传统的测量方法,如白光干涉仪和激光位移传感器。然而,这些方法在实际应用中暴露出诸多问题。白光干涉仪虽然精度较高,但对环境要求极为苛刻,在生产车间复杂的环境下,测量结果常常受到振动、温度变化等因素的干扰,导致测量误差较大。激光位移传感器则在测量透明晶圆时,由于反射光信号不稳定,难以获得准确的测量数据。这些问题不仅影响了生产效率,还导致了一定的产品次品率。
为了解决这些问题,该企业决定引入光谱共焦传感器。在安装和调试过程中,企业技术人员与传感器供应商紧密合作,根据生产线上的实际情况,对传感器进行了优化配置。他们精心调整了传感器的安装位置和角度,确保能够准确地测量晶圆的厚度。通过对测量系统的参数进行精细校准,提高了测量的准确性和稳定性。
在实际生产中,光谱共焦传感器展现出了卓越的性能。它能够快速、准确地测量晶圆的厚度,测量精度达到了亚微米级,满足了企业对高精度测量的严格要求。在测量一片厚度为 500μm 的晶圆时,光谱共焦传感器的测量误差控制在 ±0.1μm 以内,而传统测量方法的误差则在 ±0.5μm 左右。这一高精度的测量结果为企业的生产工艺提供了可靠的数据支持,使得企业能够更加精确地控制晶圆的厚度,提高产品的质量和一致性。
光谱共焦传感器还实现了对晶圆厚度的实时监测。在生产线上,传感器能够实时采集晶圆厚度的数据,并将这些数据传输到生产控制系统中。生产人员可以根据这些实时数据,及时调整生产工艺参数,如研磨、抛光的时间和力度,从而避免了因晶圆厚度偏差而导致的产品质量问题。在一次生产过程中,传感器实时监测到晶圆厚度出现了轻微的偏差,生产人员及时调整了研磨工艺,避免了这一偏差对产品质量的影响,有效提高了产品的合格率。
通过使用光谱共焦传感器,该企业的生产效率得到了显著提升。由于传感器的测量速度快,能够在短时间内完成对大量晶圆的测量,使得生产线的运行效率大大提高。同时,产品的质量也得到了有效保障,次品率显著降低。据统计,引入光谱共焦传感器后,企业的产品次品率从原来的 5% 降低到了 1% 以内,为企业节省了大量的生产成本,提高了市场竞争力。
该企业的工程师表示:“光谱共焦传感器的引入,彻底改变了我们的生产方式。它不仅提高了我们的测量精度和生产效率,还为我们的产品质量提供了有力的保障。在未来的生产中,我们将继续依赖这一先进的技术,不断提升我们的产品质量和市场竞争力。”
5.2 案例二:科研机构晶圆研究
某科研机构在新型半导体材料晶圆的研究中,面临着对晶圆厚度精确测量的挑战。该机构专注于探索新型半导体材料,以满足未来电子设备对高性能、低功耗的需求。在研究过程中,准确测量晶圆厚度对于了解材料的物理特性和性能表现至关重要。
在研究初期,科研人员尝试使用传统的测量方法,但这些方法难以满足研究对高精度和高分辨率的要求。传统方法在测量新型材料晶圆时,由于材料的特殊光学性质和表面特性,测量结果往往存在较大误差,无法为研究提供可靠的数据支持。
为了解决这一问题,科研机构引入了光谱共焦传感器。该传感器的高精度和对各种材料的适应性,使其成为测量新型半导体材料晶圆厚度的理想选择。在实验过程中,科研人员首先对光谱共焦传感器进行了校准和优化,确保其能够准确地测量晶圆厚度。他们根据新型材料的特性,调整了传感器的测量参数,如光源的波长范围、探测器的灵敏度等,以提高测量的准确性。
在测量一种新型碳化硅基晶圆时,光谱共焦传感器展现出了强大的性能。这种晶圆由于其特殊的晶体结构和光学性质,传统测量方法难以准确测量其厚度。而光谱共焦传感器通过精确分析反射光的光谱信息,成功地测量出了晶圆的厚度,测量精度达到了纳米级。这一精确的测量结果为科研人员深入研究该新型材料的性能提供了关键的数据支持。
通过对不同厚度的新型碳化硅基晶圆进行测量,科研人员发现晶圆厚度与材料的电学性能之间存在着密切的关系。随着晶圆厚度的减小,材料的电子迁移率显著提高,这一发现为新型半导体材料的优化设计提供了重要的理论依据。基于这些测量数据,科研人员能够进一步优化材料的制备工艺,提高材料的性能和稳定性。
在研究过程中,光谱共焦传感器还帮助科研人员发现了新型材料晶圆中的一些细微结构变化。通过对晶圆厚度的高精度测量,科研人员观察到在特定的制备条件下,晶圆内部出现了一些微小的分层现象。这些分层现象对材料的性能产生了显著影响,为科研人员深入研究材料的微观结构和性能提供了新的方向。
该科研机构的研究人员表示:“光谱共焦传感器的应用,为我们的研究带来了新的突破。它不仅帮助我们准确地测量了新型半导体材料晶圆的厚度,还为我们揭示了材料性能与厚度之间的内在联系,为我们的研究提供了重要的支持。”
通过这个案例可以看出,光谱共焦传感器在科研机构的晶圆研究中具有重要的应用价值。它能够为科研人员提供高精度的测量数据,帮助他们深入了解新型半导体材料的性能和特性,推动半导体材料科学的发展。
5.3 应用效果总结与经验分享
通过对上述两个实际应用案例的深入分析,可以清晰地看到光谱共焦传感器在测量晶圆厚度方面展现出了卓越的性能和显著的优势。在半导体企业的生产实践中,光谱共焦传感器的引入,如同为生产流程注入了一剂 “强心针”,极大地提高了生产效率和产品质量。其高精度的测量能力,确保了晶圆厚度的精确控制,使得产品的一致性和稳定性得到了显著提升。而在科研机构的研究工作中,光谱共焦传感器则成为了科研人员探索新型半导体材料的得力助手,为他们提供了关键的数据支持,推动了科研工作的深入开展。
在安装调试方面,与传感器供应商的紧密合作至关重要。供应商凭借其专业的技术知识和丰富的实践经验,能够为用户提供全方位的技术支持和指导。在安装过程中,供应商的技术人员可以协助用户确定传感器的最佳安装位置和角度,确保传感器能够准确地测量晶圆厚度。他们还可以帮助用户对测量系统进行校准和优化,提高测量的准确性和稳定性。在调试过程中,供应商的技术人员可以及时解决用户遇到的各种问题,确保测量系统能够正常运行。通过与供应商的紧密合作,用户可以节省大量的时间和精力,快速实现光谱共焦传感器的安装和调试。
在与生产系统集成方面,实现测量数据的实时传输和共享是关键。通过将光谱共焦传感器与生产控制系统进行无缝对接,能够实现测量数据的实时采集、传输和分析。生产人员可以根据实时测量数据,及时调整生产工艺参数,实现对生产过程的精准控制。在某半导体企业的生产线上,光谱共焦传感器与生产控制系统实现了集成,生产人员可以通过控制系统实时查看晶圆厚度的测量数据,并根据数据调整研磨、抛光等工艺参数,从而提高了产品的质量和生产效率。此外,实现测量数据的实时传输和共享,还可以为企业的质量管理和决策分析提供有力支持。企业可以通过对测量数据的分析,了解生产过程中的质量状况,发现潜在的质量问题,并及时采取措施进行改进。
在数据处理分析方面,建立有效的数据分析模型和算法能够为生产和研究提供有力支持。通过对测量数据的深入分析,可以挖掘出数据背后隐藏的信息,为生产工艺的优化和新产品的研发提供依据。在某科研机构的研究中,科研人员通过建立数据分析模型,对新型半导体材料晶圆的厚度数据进行分析,发现了晶圆厚度与材料电学性能之间的关系,为材料的优化设计提供了重要的理论依据。在某半导体企业的生产中,企业通过建立数据分析算法,对晶圆厚度的测量数据进行实时分析,及时发现生产过程中的异常情况,并采取措施进行调整,从而提高了产品的合格率和生产效率。
在实际应用过程中,还需要注意一些问题。要定期对光谱共焦传感器进行维护和保养,确保其性能的稳定性和可靠性。要加强对操作人员的培训,提高他们的操作技能和数据处理能力。要不断优化测量系统的参数和算法,以适应不同的测量需求和应用场景。
六、结论与展望
6.1 研究成果总结
本研究深入探索了光谱共焦传感器在测量晶圆厚度方面的应用,通过理论分析、实验研究和实际案例验证,取得了一系列具有重要价值的研究成果。
在理论研究方面,详细剖析了光谱共焦传感器测量晶圆厚度的原理。深入阐述了光谱共焦的基本原理,包括宽光谱光源发出复色光,经照明孔、分光棱镜后被物镜色散,以不同波长光投射到被测物体表面,聚焦在表面的波长光线反射回对应的针孔,利用表面焦点和图像平面焦点间的共轭关系计算测距值。在此基础上,深入分析了该原理在晶圆厚度测量中的具体应用,通过分析反射光的光谱信息来确定晶圆上下表面的位置,从而实现对晶圆厚度的精确测量。与其他常见测量方法如白光干涉仪、激光位移传感器等进行对比,突出了光谱共焦传感器在精度、非接触性、对透明材料适应性等方面的显著优势。
在系统搭建方面,精心设计并成功搭建了光谱共焦传感器测量系统。设计了合理的系统总体架构,包括光源、光学镜头、探测器、数据处理单元等核心组件。详细阐述了各组件的选型依据,如选用超连续谱光源作为宽光谱光源,因其能够提供丰富的波长信息,满足光谱共焦测量对多种波长光的需求;采用 CCD 探测器作为高分辨率探测器,因其高灵敏度和高分辨率的特点,能够准确捕捉反射光信号;选择合适焦距和数值孔径的物镜作为光学镜头,以保证光的色散和聚焦效果。还介绍了系统校准与标定的方法,通过使用标准厚度的晶圆对测量系统进行校准,标定波长与距离的对应关系,确保了测量系统的准确性和可靠性。
在精度优化方面,全面分析了影响测量精度的因素,并提出了有效的误差补偿与精度提升方法。深入分析了光源稳定性、光学系统像差、探测器噪声、环境温度和振动等因素对测量精度的影响。针对这些影响因素,提出了采用温度补偿算法、安装振动隔离装置、优化光学系统设计、采用先进的数据处理算法等误差补偿与精度提升方法。通过实验验证,这些方法能够显著提高光谱共焦传感器测量晶圆厚度的精度和可靠性,测量精度得到了显著提升,满足了半导体制造对高精度测量的严格要求。
在实际应用方面,通过两个实际应用案例,充分展示了光谱共焦传感器在半导体晶圆厚度测量中的卓越性能和重要价值。在某半导体企业的晶圆生产中,光谱共焦传感器的引入,提高了生产效率和产品质量,实现了对晶圆厚度的实时监测和精确控制,有效降低了产品次品率。在某科研机构的新型半导体材料晶圆研究中,光谱共焦传感器为科研人员提供了高精度的测量数据,帮助他们深入了解新型半导体材料的性能和特性,推动了科研工作的深入开展。还总结了应用过程中的经验,包括与传感器供应商的紧密合作、实现测量数据的实时传输和共享、建立有效的数据分析模型和算法等,为光谱共焦传感器的广泛应用提供了有益的参考。
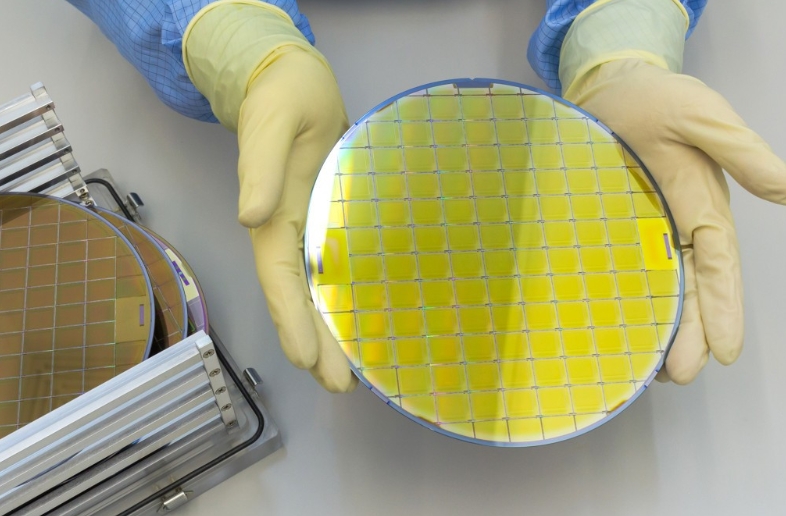
6.2 未来研究方向展望
展望未来,光谱共焦传感器在测量晶圆厚度领域还有广阔的发展空间和诸多富有潜力的研究方向。
在提高测量速度方面,随着半导体制造技术的飞速发展,对生产效率的要求日益提高。未来的研究可以致力于优化传感器的光学系统和信号处理算法,以实现更快速的数据采集和处理。通过采用更高速的探测器和更先进的信号处理芯片,能够显著缩短测量时间,满足大规模生产线上对快速测量的需求。还可以研究并行测量技术,通过同时使用多个传感器或采用多通道测量方式,进一步提高测量速度,实现对晶圆厚度的快速、高效测量。
拓展测量范围也是未来研究的重要方向之一。目前,光谱共焦传感器在测量范围上存在一定的局限性,难以满足一些特殊晶圆或复杂结构的测量需求。未来可以通过改进光学系统的设计,如采用变焦物镜或多物镜切换技术,实现对不同厚度范围晶圆的测量。研究新型的测量原理和方法,结合其他技术,如光学相干层析技术(OCT),拓展光谱共焦传感器的测量范围,使其能够测量更厚或更薄的晶圆,以及具有复杂内部结构的晶圆。
降低成本对于光谱共焦传感器的广泛应用至关重要。目前,光谱共焦传感器的成本较高,主要原因在于其核心组件的制造工艺复杂,如宽光谱光源、高分辨率探测器等。未来的研究可以聚焦于开发低成本的核心组件,通过优化制造工艺、采用新型材料等方式,降低组件的制造成本。还可以探索新的系统架构和设计方法,简化测量系统的结构,减少组件数量,从而降低整个测量系统的成本。通过降低成本,光谱共焦传感器将能够在更多的半导体制造企业中得到应用,推动半导体产业的发展。
与人工智能技术的结合将为光谱共焦传感器带来新的发展机遇。人工智能技术在数据处理、模式识别和预测分析等方面具有强大的能力。未来可以将人工智能算法应用于光谱共焦传感器的测量数据处理中,实现对测量数据的智能分析和诊断。通过机器学习算法,能够自动识别测量数据中的异常情况,预测晶圆的质量和性能,为生产过程的优化提供更准确的决策依据。利用深度学习算法,对大量的测量数据进行分析和学习,建立晶圆厚度与半导体器件性能之间的关系模型,为半导体制造工艺的优化提供更深入的指导。