一、背景与需求
在印刷、包装、金属加工等行业中,材料(如纸张、薄膜、金属薄板等)通过传送带或滚筒输送时,常因机械振动、静电吸附或操作失误导致单张材料与双张材料重叠。若未及时检测,重叠材料可能造成设备卡顿、加工精度下降甚至产品报废。传统的检测方法(如光电传感器或机械触头)易受材料透明度、颜色或表面特性的干扰,而对射式超声波传感器凭借其非接触、高适应性及强抗干扰能力,成为解决此类问题的理想选择。
二、对射超声波传感器的工作原理
对射式超声波传感器由发射器和接收器组成,发射器发出高频声波(通常40kHz~200kHz),接收器检测穿透材料的声波信号。声波在穿透材料时会发生以下变化:
信号衰减:单张材料厚度较薄,声波衰减较小;双张材料因厚度增加,声波能量被吸收或散射更多,接收端信号强度显著降低。
飞行时间(ToF):声波穿透材料的传播时间与材料厚度正相关,双张材料会延长传播时间。
通过分析接收信号的强度或传播时间差异,可精准判断材料是否为单张或双张。
三、传感器选型与参数优势
根据用户提供的传感器参数(HUA单双张检测系列),推荐以下型号及配置:
推荐型号:HUA-18GM55-200-3E1(M18尺寸,3路PNP常开输出)
关键参数:
检测范围:发射器与接收器间距20-60mm,盲区7mm,适应厚度0.01mm~3mm的材料。
输出类型:3路开关量输出(支持单双张状态分通道指示)。
响应延时:10ms,匹配生产线速度≤2m/s。
环境适应性:工作温度-25℃~+70℃,防护等级IP67,耐振动、粉尘及油污。
学习功能:通过品色线(粉色线)自适应不同材料(如纸张、金属板、薄膜)。
四、安装示意图与参数配置
安装示意图
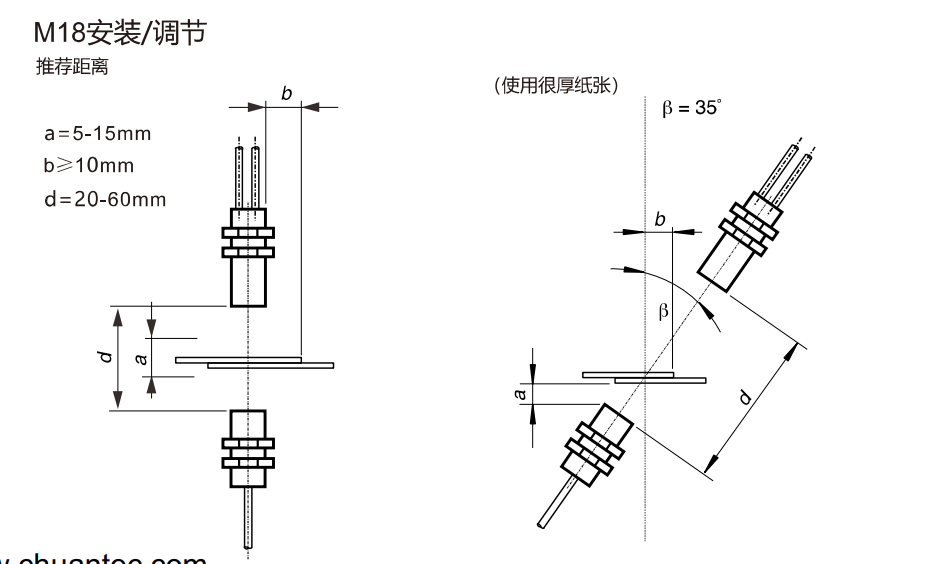
关键安装参数(以HUA-18GM55-200-3E1为例):
间距d:发射器与接收器间距设为20-60mm(根据材料厚度调整)。
安装高度a:传感器端面距传送带表面5-15mm。
角度偏差:允许与垂直方向±45°,确保声波有效穿透材料。
盲区范围:传感器前方7mm内无法检测,需避免材料进入此区域。
五、传感器学习与配置流程
单张学习模式:
短接粉色线与蓝色线(GND),通电后黄绿双灯闪烁。
放置单张材料于传感器间,绿灯闪烁后短接粉色线与GND,绿灯常亮即完成学习。
双张学习模式:
短接粉色线与棕色线(+V),切换至双张学习模式,红灯闪烁。
放置双张材料于传感器间,短接粉色线与GND,红灯常亮即完成学习。
退出学习模式:
保持粉色线与GND短接,重启传感器即可进入正常工作状态。
六、检测逻辑与系统集成
信号处理:
传感器通过声波衰减和飞行时间(ToF)判断材料厚度。
单张材料:声波衰减低,ToF短;双张材料:声波衰减显著增加,ToF延长。
输出逻辑:
单张状态:绿灯亮,输出通道1闭合(PNP高电平)。
双张状态:红灯亮,输出通道2闭合(PNP高电平)。
无材料:黄灯亮,输出通道3闭合。
系统联动:
通过PLC接收传感器信号,触发报警或分拣机构。
支持IO-Link协议,实现参数远程配置及状态监控。
七、实际应用案例:金属薄板加工生产线
场景痛点:某金属加工厂因0.5mm不锈钢薄板双张重叠,导致冲压模具频繁损坏,月均损失超5万元。
解决方案:
传感器部署:在冲压机进料口安装两对HUA-18GM55-200-3E1传感器,覆盖板材全宽。
参数配置:
间距d=40mm,安装高度a=10mm,角度偏差±1°。
响应延时10ms,匹配产线速度1.5m/s。
学习与优化:
学习单张(0.5mm)和双张(1.0mm)状态,动态阈值校准误差<2%。
结合多传感器投票机制,误检率<1%。
成效:
双张漏检率从15%降至0.5%,模具寿命延长3倍。
年节约维护成本约60万元,投资回报周期<3个月。
八、核心公式与代码片段
1. 声速温度补偿公式

2. 动态阈值计算

(Ssingle为单张信号均值,σnoise为噪声标准差)
九、总结
对射超声波传感器(如UDA系列)通过非接触式检测、多路输出及自适应学习功能,为工业单双张重叠问题提供了高可靠性解决方案。其宽检测范围、短响应时间及强环境适应性,可广泛应用于印刷、包装、金属加工等领域。未来结合AI算法优化阈值动态调整,可进一步提升复杂场景下的检测精度。